www.magyar-mernoki.com
12
'19
Written on Modified on
Csoporttechnológia: Operatív kiválóság az Ipar 4.0 korszakában
A gyártókat az ipari forradalom előtti időktől napjainkig közös cél vezérelte: adott mennyiségű alkatrészt, adott idő alatt, adott költséggel legyártani. A gyártási folyamatok a kézzel készített egyedi elemek módszerétől a gyártósorok alkalmazásáig és az egyre növekvő mennyiségű, megegyező alkatrészek előállításáig, vagyis a nagy mennyiségű/kis választékú (HVLM) eljárásokig fejlődtek. Napjainkban a programozás, szerszámgépvezérlés és munkadarab-kezelő rendszerek területén alkalmazott digitális technológia elősegíti az Ipar 4.0 néven ismert gyártási környezet kialakulását, amely lehetővé teszi rendkívül változatos alkatrészek kis tételben történő, költséghatékony gyártását: a nagy választékú/kis mennyiségű (HMLV) gyártást.
Az Ipar 4.0 korában szokás kihangsúlyozni a gyártási és digitalizálási technológiákat. Ugyanakkor a maximális termelékenység és költséghatékonyság alapja továbbra is az operatív kiválóság. A gyártók a jelenlegi gazdasági környezetben általában a gyorsaságot tekintik az operatív kiválóság fokmérőjének. A gyárba egy rajz érkezik, végül pedig egy kész munkadarab hagyja el az üzemet; a gyártók az ezen két esemény között eltelt időt a lehető legrövidebbre akarják szorítani. A gyorsaság növelésére irányuló erőfeszítések jellemzően olyan stratégiákra fókuszálnak, mint pl. a „lean” gyártás vagy a Six Sigma modell.Fontos kiemelni, hogy ezek a stratégiák általában a HVLM gyártásra vonatkoznak, és nem mindig bizonyulnak hatékonynak, amikor HMLV körülményekre alkalmazzák azokat. Az egyszerűsített HMLV gyártás egyik fontos alkotóeleme a csoporttechnológiai megközelítés, amelyben az alkatrészek megmunkálható családokba történő osztályozása és kódolása megteremti annak lehetőségét, hogy a műhely elérje a legmagasabb szintű operatív kiválóságot.
Csoporttechnológia
A csoporttechnológia egy olyan gyártásszervezési stratégia, amelyben hasonló tulajdonságok, pl. geometria, anyag, gyártási eljárás vagy minőségi szabvány szerint csoportokba vagy családokba osztályozzák az alkatrészeket, és közös gyártási módszerek alapján gyártják le azokat. A műveleteket egyéni munkadarabok helyett alkatrészcsaládokra tervezik meg.
Sok esetben, amikor a gyártást alkatrészcsaládok feldolgozására szervezik meg, az elrendezést sejtszerű gyártásként írják le. A sejtszerű gyártás 1980-ban vált meghatározóvá, nagyjából akkor, amikor megkezdődött a HMLV gyártás korszaka. A gyártók felismerték, hogy a tételek mérete csökkenésnek, a munkadarabok változatossága és az új munkadarabok száma pedig növekedésnek indult. A gyáraknak szembesülniük kellett a viszonylag kis tételben gyártott különféle munkadarabok sokféleségével. Az előkészítésre és gyártásra fordított idő exponenciális növekedésnek indult, a gyártók pedig igyekeztek mindezt kézben tartani.
A csoporttechnológiai alkatrészcsaládok létrehozása az alkatrészek kodifikációján és osztályozásán alapul. Az egyes alkatrészekhez egy betűkből, számokból vagy ezek kombinációjából álló kódot rendelnek hozzá, ahol az egyes betűk vagy számok a munkadarab egy adott jellemzőjére, vagy az előállításához szükséges gyártási technikára utalnak. Az 1. ábrán az alkatrész kódjának 6. számjegye a munkadarab méreteit, 7. számjegye a nyersanyagot, 8. számjegye a munkadarab eredeti alakját, 9. számjegye pedig az előírt minőségi szintet jelenti. A 3–5. számjegy írja le az alkarész megmunkálásához szükséges műveleteket.
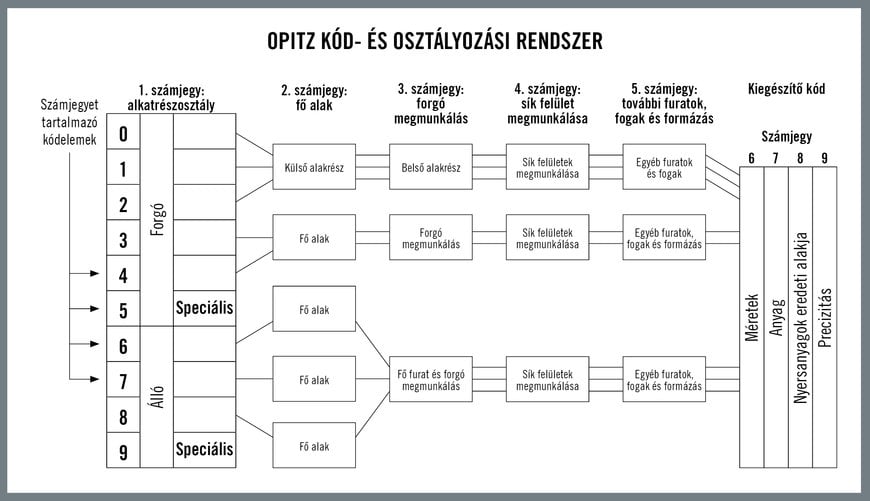
1. ábra:
HQ_ILL_Opitz_Coding_And_Classification_System.jpg
Az alkatrészkódokat a gyártástervezéshez és árajánlat-készítéshez használják egy képzeletbeli vagy nem létező alkatrészre hivatkozva, amelyet összetett munkadarabnak hívnak, amint az a 2. ábra második sorában látható. Az összetett ebben az esetben nem a bonyolultságra utal; egy általános munkadarab példáján keresztül szemlélteti a cég profiljába tartozó összes előállítható jellemzőt, pl. nagy és kis pontosságú furatokat, mély vagy sekély zsebeket, kontúrmarásokat stb. Az ábra első sora olyan munkadarabokat vázol, melyek a második sorban szereplő összetett munkadaraboknál leírt műveletek alkalmazásával legyárthatók. A szükséges jellemzők előállításához igényelt gyártási költségeket összeadva megkapjuk a teljes költséget, ami egyszerűbbé teszi az árbecslést. Nincs szükség a költség alkatrészenkénti, egyedi elemzésére.
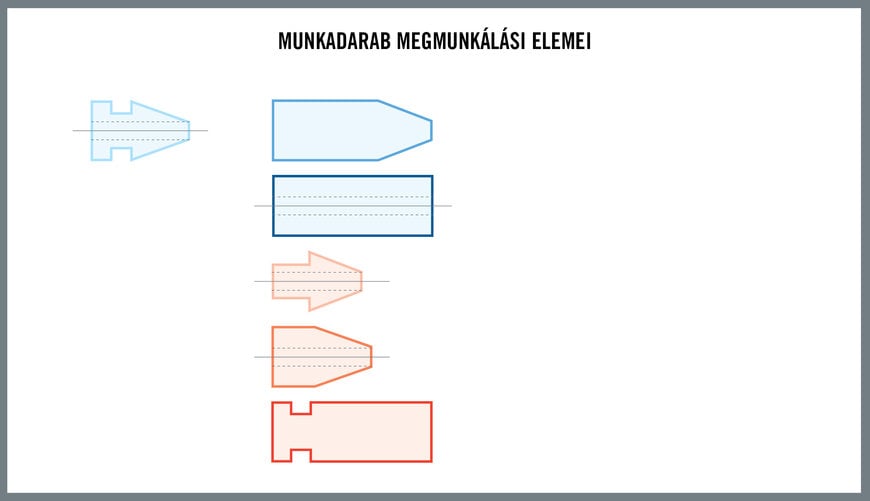
2. ábra:
HQ_ILL_Workpiece_Machining_Elements.jpg
A munkadarab rajzán gyártástervezők és értékbecslők dolgoznak, hogy a munkadarab jellemzőinek az összetett munkadarabbal való összevetése alapján dolgozhassanak ki árajánlatot. Emellett olyan egyéb gyártási elemeket is meghatároznak, mint hogy milyen szerszámgépekre van szükség, alkalmazni kell-e hűtőfolyadékot stb. Ezen kívül a fejlett CAM rendszerek segítségével megvalósított csoporttechnológiai eljárások tovább csökkentik a gépi megmunkálást megelőző tervezés időigényét. A további előnyök között szerepel a gyári részlegek közötti kommunikáció továbbfejlesztése is, hiszen mindannyian ugyanazon összetett munkadarabmodell alapján végzik a munkájukat.
A csoporttechnológiai megközelítés kezdetben a kifejlesztésén dolgozó személyek tapasztalatain alapult, amit folyamatmérnökökkel, programozókkal és tervezőkkel folytatott, a különféle gyártási műveletek árával kapcsolatos beszélgetések során gyűjtöttek össze. Bár a fejlesztés az 1980-as években elkezdődött, az egyedi tapasztalatok összegzése, és az adatok rendszerbe szervezése olyan folyamat volt, amely napjaink mesterséges intelligenciával kapcsolatos kezdeményezéseire emlékeztet.
Bizonyos esetekben a csoporttechnológia a műhely átszervezését igényli. A 3. ábra bal oldalán láthatók az alkatrészek által a műhelyben bejárt olyan kerülőutak, amelyek az esztergálást, marást és köszörülést tartalmazó hagyományos gépi funkciókból álló elrendezésen alapulnak. Ugyanakkor, ha az ábra jobb oldalán látható módon a munkadarabok családokba vannak csoportosítva, és a megmunkálásuk sejtszerű elrendezés alapján történik, a szerszámgépek a gyártási folyamatok és az alkatrészek műhelyben történő mozgásának egyszerűsítése alapján helyezhetők el. Minden munkadarabcsalád megmunkálása a leghatékonyabb módon, a műhelyen belüli felesleges mozgatás nélkül történik. Ennek eredményeként jelentősen csökken az alkatrészek előállításához szükséges idő.
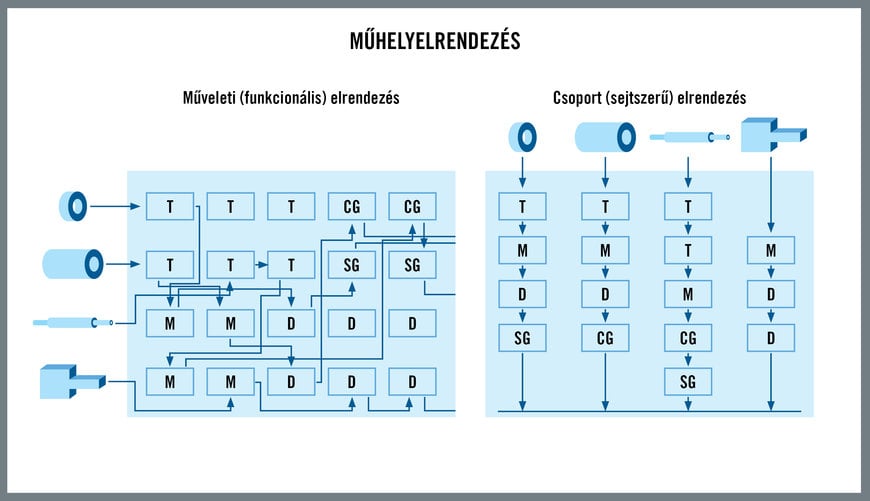
3. ábra:
HQ_ILL_Workshop_Layout.jpg
Ahogy az lenni szokott, az új koncepció bevezetése előnyöket és kihívásokat is tartogat. A csoporttechnológián alapuló megközelítés előnyöket jelent a megmunkálásban, folyamattervezésben és a gyártáshoz szükséges idő lerövidítésében, de lehetséges kihívásokat is felvet. Először is a csoporttechnológián alapuló megközelítés bizonyos mértékig csökkenti a rugalmasságot. A hagyományos műhelyelrendezés rugalmasabb, ha egy adott munkadarab-konfigurációra szóló igény jelentős megnövekedése miatt csökken a gyártási keresztmetszet. A hagyományos elrendezésben a részleg más gépei is használhatók az alkatrészek előállítására. Másrészről pedig a gépi állásidők kezelése szintén kihívást jelenthet. Ha egy alkatrészcsalád iránti igény ideiglenes csökkenése tapasztalható, a sejtszerű elrendezésben használt gépek munka nélkül maradnak.
A csoporttechnológiai koncepciók alkalmazásából fakadó másik lehetséges probléma az egyes kódrendszerek összevetésének általánosan rendkívül időigényes folyamata. Az adott kódrendszernél azonban fontosabb, hogy a cégnek alaposan ismernie kell berendezéseit és erőforrásait, illetve az elérni kívánt eredményeket. Ebben az esetben a házon belül létrehozott kódrendszer egyszerű és hatékony megközelítésnek bizonyulhat. A műhelynek az alkatrészcsaládok hatékonyabb megmunkálása érdekében történő átrendezése egy másik létesítményspecifikus döntés. A nagyobb cégek könnyebben átrendezhetik gépeiket, míg a kisebb vállalatok gazdasági korlátokkal és egyéb tényezőkkel szembesülhetnek.
Gyorsabb, pontosabb árajánlatok
Az alkatrészekre vonatkozó árajánlatok készítésének csoporttechnológián alapuló megközelítése növelheti mind az árbevételt, mind pedig a nyereséget. Vegyünk például egy HMLV gyártási környezetben tevékenykedő repülőgépipari alvállalkozót, egy és öt közötti munkadarabos tételmérettel, aki évente 4000 árajánlatkérést kap. Mivel az egyes alkatrészekre vonatkozó ajánlatkérések elemzésére nem jutott elég idő, az ajánlattételi folyamat lelassult, a műhely pedig a lehetséges 4000 helyett csak 1500 komoly árajánlatot tudott tenni. Kb. 2600 megrendelés érkezett be. Ezt követően a csoporttechnológiai kezdeményezések által támogatott elemzés használatának, valamint a munkadarabokra vonatkozó részletes információkon alapuló alkatrész-árajánlatoknak köszönhetően az alvállalkozó évente 3000 komoly ajánlatot tudott adni. A több komoly ajánlat több megrendelést eredményezett, elérve az évi 3200 darabos szintet. Ami pedig a legfontosabb, a bekerülési költségen és nyereségen alapuló ajánlatok átlagosan több mint 30 százalékkal olcsóbbnak bizonyultak mint a csoporttechnológiai koncepciók bevezetése előtt készült ajánlatok.
A gyorsabb és pontosabb ajánlatkészítési folyamatnak két előnye volt. Csökkent a haszonkulcsot negatívan érintő hibás alákínálások, és az ügyfeleket elbátortalanító, pontatlanul magas árajánlatok száma. A csoporttechnológiai koncepciók bevezetése több beleszólást biztosított a gyártónak azzal kapcsolatban, hogy mit és mennyiért gyártson, így csökkentve a pontatlan ajánlatokból fakadó problémák mennyiségét.
A csoporttechnológia elvét követve az egyes munkadarabok és gyártási paraméterek alapos megtervezése helyett a hasonló jellemzőkkel rendelkező alkatrészeket csoportosítják, és együtt munkálják meg. Jó példa erre a megközelítésre, amikor egy műhely szíjhajtású erőátviteli rendszerekhez tárcsákat gyártott. A különböző felhasznált szíjak esetén tárcsáról tárcsára változtak az átmérők, szélességek és szíjvezető profilok. A különböző konfigurációk közötti csereidő másfél óra volt.
A folyamatok elemzése során kiderült, hogy a tárcsák közötti minden egyes csere során a gépet teljesen szétszerelték, az összes szerszámot eltávolították, megtisztították és a raktárba helyezték. A következő tárcsa megmunkálásához ugyanazon szerszámok többségét visszaszerelték a gépre. A csoporttechnológián alapuló megközelítés esetén a nem egyforma, de hasonló kerekeket egy családba csoportosították. A teljes csereidő az NC program lecseréléséből, néhány megmunkálási paraméter módosításából, illetve a horony profilját megmunkáló szerszám időnkénti cseréjéből tevődött össze. A munkadarabtól függően a csereidő másfél óráról tíz percre csökkent. A legnagyobb kihívás a műhely személyzetének meggyőzése volt, miszerint a gyártott alkatrészek ugyanahhoz a családhoz tartoznak, és ennélfogva gyorsabban megmunkálhatók.
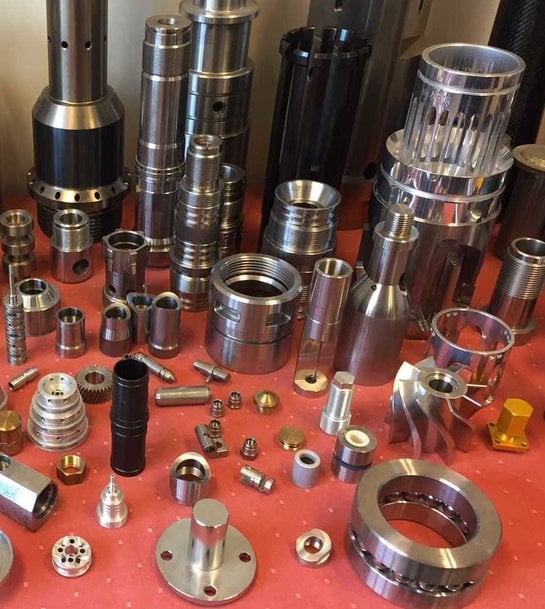
HQ_IMG_Different_Workpieces.jpg
Összegzés
A csoporttechnológián alapuló gyártásszervezési stratégia (amellyel kapcsolatban Dave Morr, a SECO ausztráliai leányvállalatának szakértője, kiterjedt fejlesztési munkát végzett) segíti a gyártókat a HMLV gyártás kihívásainak hatékony kezelésében. A hagyományos termelékenységnövelő stratégiák, mint például a „lean” gyártás és a Six Sigma modell, bizonyított előnyökkel jár, különösen a HVLM gyártás területén, ahol a műveletek az azonos alkatrészek hosszú gyártási folyamata során finomhangolhatók. Mindamellett a nagyon változatos, kis tételben történő gyártás jelentősége tovább nő a gépgyártás technológiájában, illetve a digitális termékfejlesztésben és -kezelésben tapasztalható fejlődésnek köszönhetően. Az alkatrészek családokba sorolásának és az árképzési, illetve megmunkálási műveletek konszolidációjának köszönhetően a csoporttechnológián alapuló megközelítés az Ipar 4.0 kihívásainak hatékony kezelési módját kínálja a gyártóknak.
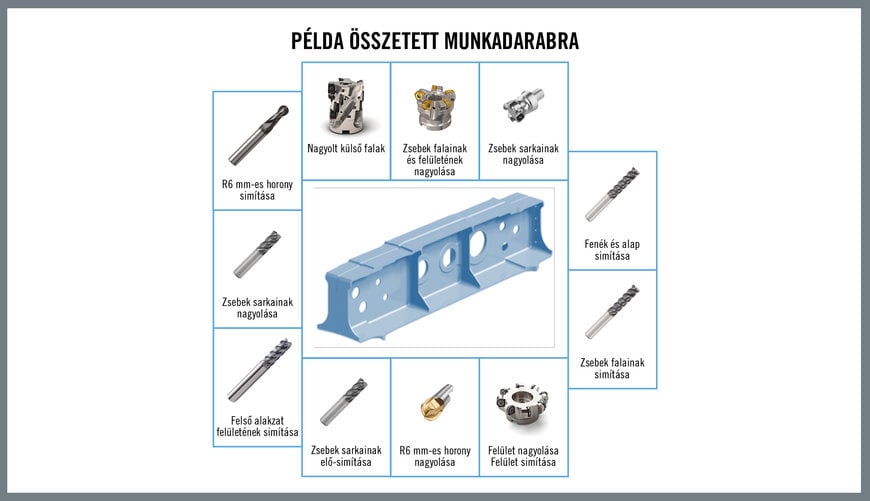
4. ábra:
HQ_ILL_Example_Of_Complex_Workpiece.jpg
Oldalsáv
Csoporttechnológia és Seco Consultancy Services (SCS) szolgáltatások
A csoporttechnológián alapuló gyártás szervezési stratégiája az operatív kiválóság elérésének egyik fontos tényezője, és a gyártó általános tevékenységének is fontos eleme lehet. A verseny ugyanakkor sok gyártót arra kényszerít, hogy szinte kizárólag adott mennyiségű alkatrész, adott időre, adott költség melletti előállítására fókuszáljon, és nincs elég idő, illetve szakértelem az üzleti folyamatok és gépi megmunkálási műveletek pontos elemzésére és optimalizálására.
A Seco létrehozott egy olyan új részleget, melynek célkitűzése, hogy segítse az olyan közepes méretű cégeket, amelyek rendelkeznek a gyártási fejlesztések alkalmazásához szükséges erőforrásokkal, de nincs elég tőkéjük folyamatfejlesztő mérnökök alkalmazására vagy egy nagy üzleti konzultációs céggel való együttműködésre. A Seco Consultancy Services (SCS) a megmunkálás hatékonyságával és gazdaságosságával segíti a gyártókat a gyártási és üzleti vonatkozású problémáik kiegyensúlyozásában. Az SCS márkasemleges, és a felhasználó meglévő szerszámaival dolgozik, függetlenül azok márkájától.
Az SCS előnyeinek kihasználására irányuló első lépés a gyártás hatékonyságának felmérése (MEE), amely a megmunkálás, illetve a gyártórendszerek és a teljesítmény elemzését tartalmazza.
Az SCS elemzi a cég adottságait, és megvizsgálja az előkészítésben, megmunkálásban és a berendezésekben tapasztalt problémákat. Feltárják az adottságokra és vagyonelemekre, illetve az alkalmazottak hiányos tudására vonatkozó problémák alapvető okait. Az előkészítés elemzése magába foglalja a programozás támogatását, illetve a módszerek és alkatrészek szabványosítását. Feltárják a megmunkálási problémákat, és a módszerek optimalizálásával, illetve a hibaelhárítással kezelik azokat. A raktárkészletet és a felhasználást vizuális formában megjelenítő és a szerszámokat felügyelő programok megoldást kínálnak a gépkezelési problémákra.
Az SCS program keretein belül a Seco Technical Education Services (STEP szemináriumok és kurzusok formájában) segítséget kínál, és képzést biztosít a cég alkalmazottainak. A szolgáltatás fő eleme a műhelyszemélyzet meggyőzése az új stratégiák bevezetéséről. Az új elgondolást és rendszert leíró plakátok kiragasztásának minimális hatása van. Mégpedig azért, mert a probléma leggyakrabban nem a tudással van, hanem azokkal az alkalmazottakkal, akik meg vannak győződve arról, hogy a hagyományos megoldások a legjobbak. A siker kulcsa, hogy az alkalmazottak felismerjék az új stratégia előnyeit, és rendelkezzenek a szükséges fegyelemmel azok bevezetéséhez.
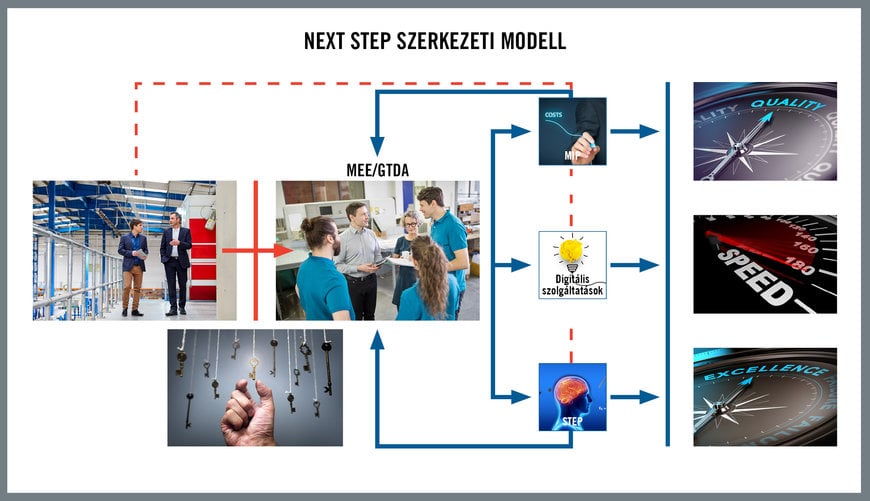
5. ábra:
HQ_ILL_Structural_NEXT_STEP_Model.jpg
Szerzők:
Patrick de Vos, vállalati műszaki oktatási vezető, Seco Tools
További információkért kérem forduljon …