www.magyar-mernoki.com
03
'18
Written on Modified on
Napjaink gyártási termelésgazdálkodásának valósága
A gyártóműhelyek adott idő alatt, adott költségek mellett, adott számú, meghatározott minőségű alkatrészt kívánnak gyártani. E célok következetes megvalósítását különféle tényezők, mint például a forgácsolási paraméterek, a szerszámköltségek és átállási idők, a szerszámgépek kihasználtsága, a munkadarabok kezelési költségei, illetve az anyagköltségek és munkabérek befolyásolják.
A termelésgazdálkodás a kívánt eredmények eléréséhez szükséges folyamati tényezők egyensúlyának megtalálására irányuló szakma és tudomány. A gépi megmunkálás több mint két évszázados történelme során a termelésgazdálkodás összetevőinek száma megsokszorozódott. A gyártás először a cikkek kézműves elkészítésétől a szabványosított alkatrészek szerszámgépesített tömeggyártásáig fejlődött. A gyártási módszerek javulásával létrejött a tömegtermelés második generációja, ahol már szerepet kaptak a gyártósorok, illetve az azonos alkatrészek előállításának egyre fokozódó üteme: a nagy mennyiség, kis választék (HVLM) elve. Ezt követően a CNC-gépek és robotok elhozták a tömeggyártás hatékonyságának harmadik generációját. Legújabban pedig a programozásban, szerszámgépvezérlésben és a munkadarab-kezelő rendszerekben alkalmazott digitális technológia átvezet a gyártás negyedik generációjába, az Industry 4.0 korszakába, amikor is lehetővé válik a költséghatékony, nagy választékú, kis mennyiségű (HMLV) gyártás.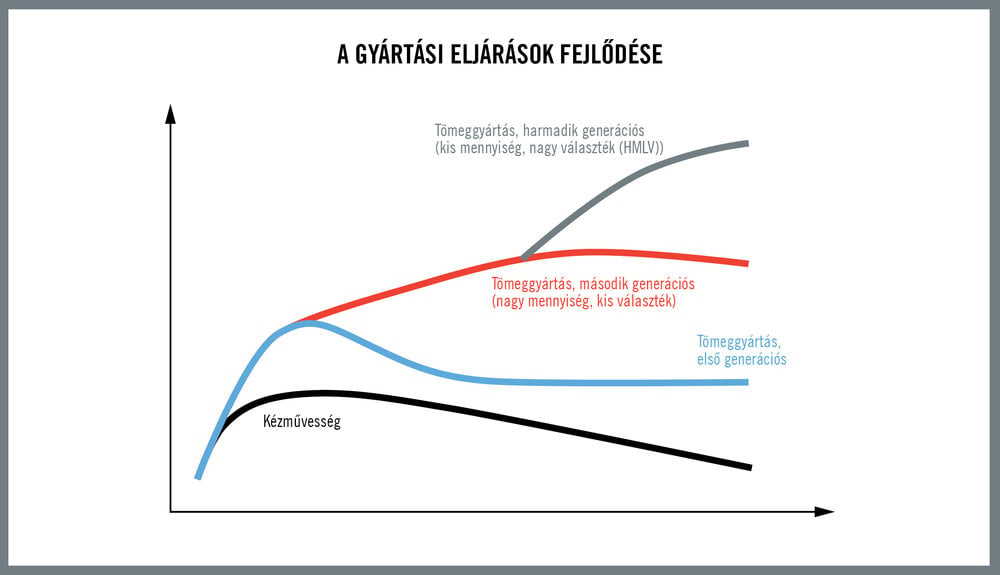
HQ_POS_Manufacturing_Process_Evolution.jpg
A HVLM és HMLV gyártás közötti átmenet hatékony megvalósításához nélkülözhetetlen, hogy a gyártók felismerjék a megváltozó és fejlődő termelésgazdálkodási lehetőségeket, és kihasználják a működésük értékelését, illetve céljaik elérését biztosító információkat és technológiákat. Az átmenet kulcsfontosságú eleme a szakítás a túlságosan leegyszerűsítő hiedelmekkel és gyakorlattal, illetve a termelékenység maximalizálására irányuló törekvéseket aláaknázó rejtett költségek feltárása.
Nagy mennyiség, kis választék, egyszerű gazdálkodás?
A felcserélhető alkatrészekből álló, hasonló termékek gyártásának felgyorsításához a 19. században szabványosított gépi megmunkálási folyamatokat vezettek be. A HVLM-rendszer az autóipari gyártás során finomult ki mai formájára, a több százezer vagy több millió hasonló alkatrész éveken át történő gyártására szolgáló gyártósorok felállításának és egyéb módszereknek köszönhetően.
A HVLM gyártás hosszú távú természetéből fakadóan a gyártók finomhangolhatják a maximális termelékenység, és alacsony ár elérésére irányuló tevékenységeket. A kiegészítő technológiák, például a palettacserélők és robotok tovább csökkentik a változékonyság mértékét. Feltételezhető, hogy a gyártás tökélesen zajlik, és 100 százalékos hozamot biztosít, előre kiszámolható költségekkel, leállások, selejt, újbóli gyártás és másodlagos műveletek, például sorjázás nélkül.
Az egyik feltételezés az, hogy a szerszámköltség általában a teljes gyártási költség három százaléka. Ez az érték kényelmes referenciaértéknek mondható, de ritkán tükrözi a valóságot. A munkadarabok anyagmegmunkálási jellemzői például komoly befolyásoló tényezők; az acélról titánra váltva egy alkatrész megmunkálása ötszörösére növelheti a szerszámhasználatot. Ha minden egyéb ugyanaz, a három százalékos arány 15 százalékra nő.
Kizárólag a szerszámok használati idejét alapul véve más tényezők, például a szerszámcserekor fellépő állásidők figyelmen kívül maradhatnak. Ez a megközelítés jelentős mértékben elfedi a valóságot. A gyártóknak tudomásul kell venniük, hogy a szerszámozási idő, beállítási idő, szerszámváltási idő, a betöltés, ürítés és egyéb tényezők mind hatással vannak egymásra.
A folyamatok tényezőinek nem várt egymásra hatására egy egyszerűsített példa, amikor egy műhely egy két perc forgácsolási időt, és összesen két perc betöltési és ürítési időt igénylő alkatrészt munkál meg. A szerszámváltás egy percet vesz igénybe, a szerszám élettartama pedig öt munkadarab, ami 0,2 perces alkatrészenkénti csereidőt eredményez. Mivel minden alkatrész 4,2 perc feldolgozási időt igényel, óránként alig több mint 14 munkadarab készül el. Minden szerszám ára 15 euró, az öt munkadarabos szerszámélettartam miatt 2,8 szerszám (42 euró) szükséges 14 munkadarab legyártásához. A szerszámgépnek 50 euró/óra költsége van. Összegezve, 14 munkadarab egy órán belül történő elkészítése 92 euróba kerül.
A termelékenység fokozása érdekében a műhely 10 százalékkal növeli a forgácsolás sebességét. Ez 10 százalékkal (1,8 percre) csökkenti a forgácsolás idejét, de a szerszám élettartamát is durván a felére csökkenti, ami azt jelenti, hogy egy vágóél csak két és fél munkadarabot készít el, mielőtt cserére szorul. A szerszámcsere ideje még mindig egy perc, míg a munkadarab betöltési/ürítési ideje két perc. Egy munkadarab legyártásának ideje továbbra is 4,2 perc (1,8 perc forgácsolási idő, 2 perc munkadarab-kezelés és 0,4 perc szerszámcsere), azaz 14 munkadarab óránként. A szerszámgép és a szerszámok költségei ugyanazok, de most már 5,6 szerszám (84 euró szerszámköltség) szükséges egy óra működéshez. A termelékenység növelésére irányuló kísérlet ellenére a 14 munkadarab gyártási ideje változatlan marad, de a költségek 92 euróról 134 euróra emelkednek.
Ebben az esetben a forgácsolás sebességének fokozása nem teszi termelékenyebbé a munkafolyamatot. A forgácsolási idő megváltoztatása a megmunkáló rendszer más tényezőire is hatással van, példánkban a szerszám élettartamára és a szerszámcsere idejére. Ennek értelmében a műhelynek gondosan figyelembe kell vennie a művelet megváltoztatásának összes következményét.
A rejtett költségek másik jellemző előfordulási helye a munkafolyamatok végrehajtása. Sok műhely esetében például a lapkacserére fordított idő számít a rejtett költségek tankönyvi példájának. Egy lapka cseréjére megszabott idő például lehet, hogy egy perc. Amikor azonban azt a műhelyben ténylegesen megmérik, az akár két, három vagy tíz perc is lehet, ami 60 és 600 másodperc közötti különbséget eredményez.
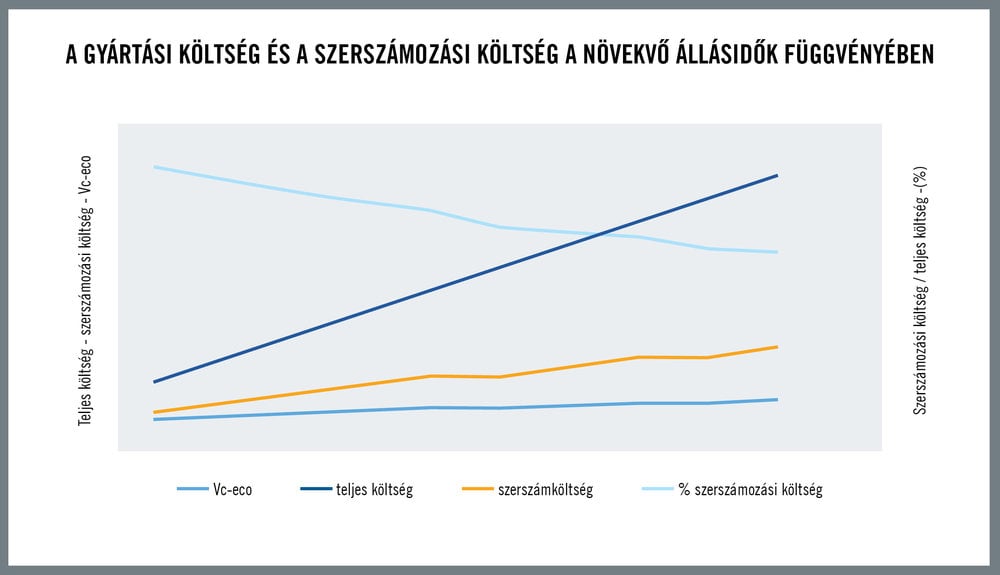
HQ_ILL_Production_Cost_And_Tooling_As_A_Function_Of_Increasing_Idle_Times.jpg
2. ábra
Nagy választék, kis mennyiség, összetett szempontok
Napjaink globális versenye arra ösztönzi a gyártókat, hogy a felhasználók kisebb csoportjai igényeinek kielégítésére termékeiket többféle változatban gyártsák. A fejlett számítástechnika lehetővé teszi az alkatrésztervek és gyártóprogramok gyors módosítását, illetve a termékváltozatok és a raktárkészlet egyszerű követésére is módot teremt. Ez a szélesebb választék alacsonyabb mennyiség (HMLV) gyártásra történő átállást eredményezi. Ez a megközelítés napjainkra annyira kifinomulttá vált, hogy lehetővé teszi egyszámjegyű vagy akár egyetlen terméket eredményező gyártási folyamatok bevezetését is.
A HVLM gyártás szélesebb időhorizontja lehetővé teszi a folyamatok tényezőinek átgondolt tervezését és finomhangolását. A HMLV folyamatok tervezése ettől eltérő. A számítógépes tervezési és készletkezelési technológiák támogatják a terméktípus és kimenet gyors módosításait, ennek eredményeként azonban a HMLV tervezési folyamat összetett és reaktív. Egy tíz alkatrészre szóló megrendelést követhet két, öt vagy akár egyetlen elemre szóló, rengeteg különféle alkatrészre vonatkozó rendelés is. A munkadarabok anyaga acélról alumíniumra vagy titánra, az alkatrészek geometriája egyszerűről összetettre változhat. Nincs elég idő a szerszámok élettartamának kísérletezéssel történő megállapítására.
A HMLV folyamatok szerszámélettartamának kezelésekor a műhelyek általában konzervatív becsléssel élnek a szerszám élettartamára vonatkozóan, és a biztonság kedvéért minden gyártási folyamatra új szerszámmal számolnak, jóval a termelékenységi élettartam előtt selejtezve azt. A forgácsolási idő csak egy szelete az összképnek. A HMLV gyártás során a különböző munkadarabok kezelése, a szerszámok és a lapkák cseréje gyakran hosszabb ideig tart, mint a forgácsolás tényleges időtartama. A szerszámok, szerszámgépek, állásidők, ráfordított munka és a munkadarabok anyagai rejtett költségeket tartalmazhatnak. A termelésgazdálkodás legújabb megközelítése a szerszámok és munkadarabok anyagköltségeit, a berendezések és a gyártás költségeit, a leállások alatti berendezésköltségeket és a bérköltséget, illetve karbantartási költségeket is figyelembe veszi.
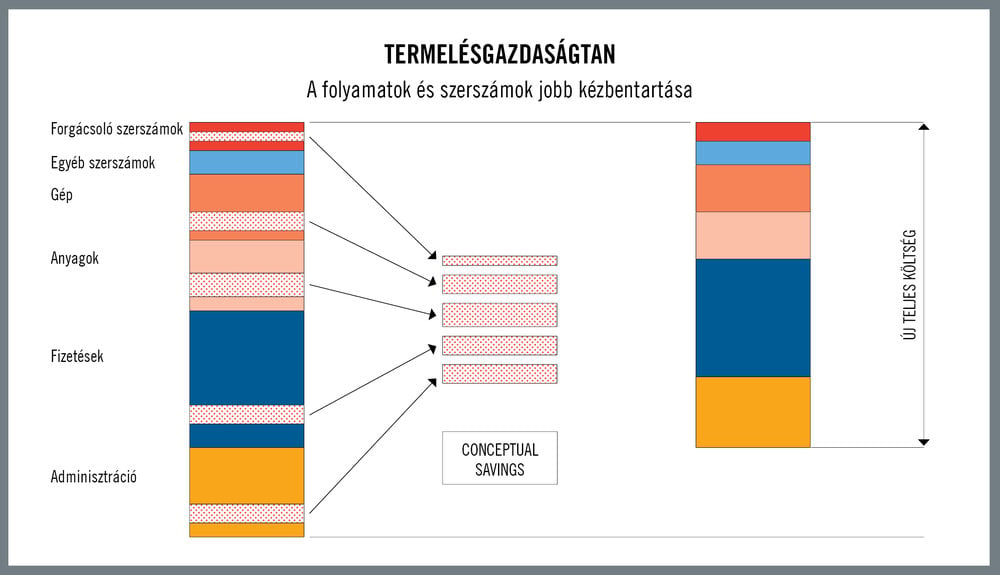
HQ_ILL_Production_Economics
3. ábra
A gyorsan változó HMLV termékkövetelmények fokozzák a százalékosan magas hozamú termelés elérésének nehézségeit. Hosszú távú HVLM termelés esetén a kísérletezgetések és változtatások a felső kilencven százalékos tartományban mozgó hozamokat eredményezhetnek. Ezzel szemben a HMLV hozamok két véglet között mozoghatnak. Egyetlen alkatrész sikeres gyártási folyamata 100 százalékos hozammal is járhat, ha viszont az alkatrész elfogadhatatlan vagy a munkadarab selejtes lesz, az nulla hozamot eredményez. A minőségre, a költségekre és az időre vonatkozó hatékonysági igények ugyanazok maradnak, de a legfontosabb követelmény az eredmény, már az első próbálkozásra. Ilyenkor a legfontosabb szempont a szerszámtörés elkerülése. Az egyik előny az, hogy a szerszámkopással rövid sorozatoknál minimális szinten kell foglalkozni, észszerű határokon belül pedig agresszívabb és termelékenyebb forgácsolási paraméterek alkalmazhatók.
Egy ide vonatkozó változó határozza meg a szerszámcsere legalkalmasabb időpontját. A túl hosszú várakozás szerszámtörést és mindenképpen a gyártás leállását, de akár a munkadarab sérülését is eredményezheti. Másrészről viszont a szerszám túl gyakori cseréje a szerszámköltségek, továbbá a gépleállások és szerszámcsere miatti időveszteség okán gyakran megnöveli a költségeket. A szerszámcserék szükséges időpontjának meghatározásához meg kell vizsgálni, hogy a váltás miként befolyásolja a teljes megmunkálási rendszert, meg kell alkotni a csereprotokollt, majd szigorúan be kell tartani azt.
Összegzés
A fémforgácsoló rendszerek elemei nem egy az egyben kapcsolódnak egymáshoz. A forgácsolás feltételeinek, a munkadarab anyagának vagy a termék mennyiségének megváltozása hatással van a szerszámok élettartamára és a gépi megmunkáló rendszerek számos egyéb tényezőjére. A gyártóüzem számára a gyártásgazdálkodás legnagyobb kihívása felismerni ezeket az összefüggéseket, és olyan stratégiákat kifejleszteni, amelyek lehetővé teszik az ezekkel kapcsolatos pragmatikus munkavégzést. Sajnos nem lehet minden gyári dolgozó matematikaprofesszor, akiknek egyébként sincs idejük mélyebben elemezni az összefüggéseket. Ennek eredményeként a beszállítók olyan folyamatelemző és -felügyelő szolgáltatásokat kínálnak (lásd az oldalsávot), amelyek tájékoztatják a gyártókat műveleteik teljes spektrumáról, és iránymutatást adnak erőfeszítéseik termelékenységének, illetve gazdaságosságának maximalizálásához.
A műhelytulajdonosok gyakori panasza, hogy rengeteg munkájuk és fizető ügyfelük van, de mégis veszteségesek. A megoldás a problémáikra, hogy felismerjék a napjaink termelésgazdálkodásában szerepet játszó tényezőket, illetve felfedjék és kizárják a figyelmen kívül hagyott és
rejtett költségeket, maximalizálva ezáltal gyártási folyamataik jövedelmezőségét.
Oldalsáv
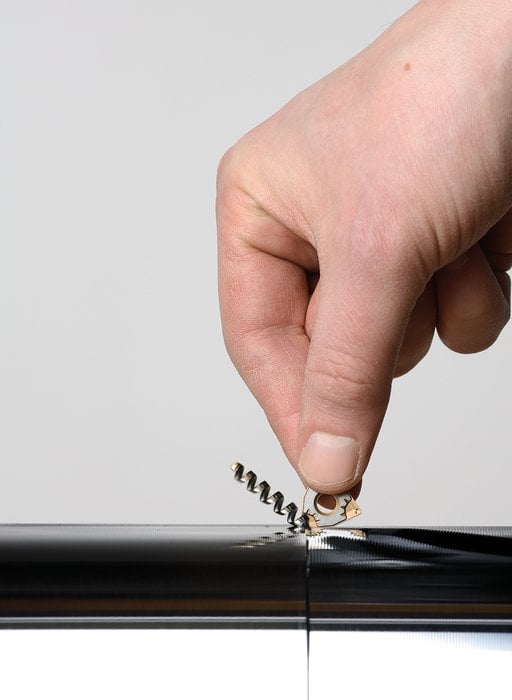
HQ_IMG_Duratomic_Chip.jpg
4. ábra
Automatizált elemzés
A tömegtermelés elindulásától számítva a gyártási termelékenységet és költségeket befolyásoló tényezők száma a sokszorosára nőtt. Ahogy a gépi megmunkálási műveletek és berendezések egyre összetettebbé váltak, ez a gyártórendszerek elemei közötti összefüggésekről ugyanígy elmondható. Egyik elem sem létezik önmagában; például a gyártási kapacitással kapcsolatos követelmények megváltozása hatással van a szerszámozás, a berendezések, a karbantartás, a munka és egyéb tényezők költségére
Az érintett tényezők számának és egymáshoz való viszonyának meghatározása önmagában is komoly kihívás. Az összetettség a gyártási folyamatok mérésének, szabályozásának és felügyeletének rendszerszintű megközelítését igényli.
A Seco termelékenység- és költségelemzési (PCA) rendszere a teljes gyártási folyamatot megvizsgálja, hogy meghatározhassa a költségcsökkentés és termelékenységnövelés módszereit. A rendszer alapját a Seco évtizedek alatt felhalmozott, globális gyártási tapasztalata és ismeretei képezik. A Seco ezt a tudást kombinálja a kifinomult számítógépes elemzéssel és a Monte Carlo szimulációs technikát is magában foglaló algoritmusokkal, lehetővé téve ezáltal az automatikus költségmodellezést
A szakképzett Seco-képviselő elvégzi a PCA-t, amely a folyamat során használt összes szerszámot és technológiát kiértékeli, hogy egy átfogó, a folyamatok információit, például a szerszámozási és forgácsolási adatokat, illetve a költséginformációkat, ideértve az alkatrészenkénti költséget, óránkénti termelési mennyiséget és befektetési költséget tartalmazó jelentést készítsen. A PCA képes az egyetlen géppel végzett szerszámműveletektől a gyártóműn áthaladó munkadarab teljes útvonaláig történő folyamatok elemzésére is.
A rendszer a költségeket leginkább befolyásoló termelékenységfokozásra fókuszál. Figyelembe veszi a szűk keresztmetszeteket és működési korlátokat, és felismeri, hol van szükség átfogóbb elemzésre.
A tárgyi működésre vagy üzemre vonatkozó idő- és költségreferenciákból készült tanulmányok alapján a PCA szoftver áttekinti a szerszámozási tényezőket, beleértve a folyamatok paramétereit, a ciklusidőket és az átviteli követelményeket is. A második szakasz ugyanazt a folyamatot foglalja magában, de a forgácsolási feltételek és az alkalmazott szerszámok tekintetében módosításokat eszközöl. A harmadik szakaszban a folyamat megváltoztatására, műveletek egyesítésére és nagyobb változtatásokra, például szerszámgépek frissítésére is sor kerülhet.
A Seco PCA rendszerét használó gyártók ágazattól függetlenül általában 30 százalékos költségmegtakarításra és 40 százalékos termelékenységnövekedésre számíthatnak.
Szerzők:
Patrick de Vos, vállalati műszaki oktatási vezető, Seco Tools
További információkért kérem forduljon …